
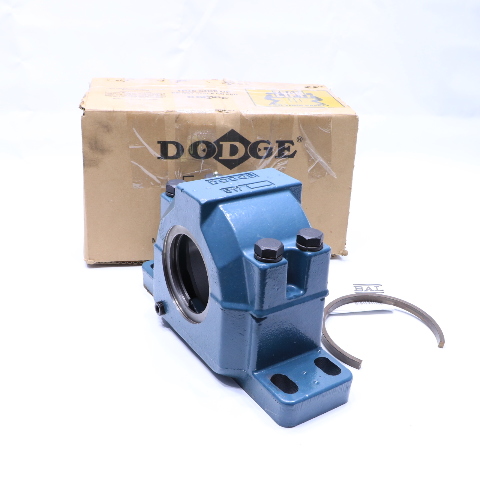
- #Mitsubishi plc serial communication protocol how to#
- #Mitsubishi plc serial communication protocol Pc#
- #Mitsubishi plc serial communication protocol windows 7#
- #Mitsubishi plc serial communication protocol series#
This is fine for connecting to a printer or sending simple information to another device but the overall communication speed is limited by the scan time. When communication is with the RS instruction in the ladder logic you must program in the complete send and receive string for each data point. If you add a RS232 BD board or a communications add-on block plugged into the PLC you can communicate with the PLC on the program side using instructions written in the ladder program. A computer connected to the front port can read or write to every bit or register in the PLC. The “front” port is where you connect a computer for programming or an HMI and no programming is necessary in the ladder logic for communication. Mitsubishi considers the protocol proprietary. Using the RS422 port and talking to the “processor” side requires special software. But all this specification is of Serial port.
#Mitsubishi plc serial communication protocol series#
I have downloaded some protocol specification of FX series PLC. Things have moved on insce OP and I'm on LabVIEW 2013.
#Mitsubishi plc serial communication protocol how to#
I'm also stuck for a driver or an exampe of how to talk MC protocol to a Mitsubishi MELSEC-F containing FX3U-ENET. The RS422 is used to talk to the PLC on the “processor” side. In our project we need to communicate with the FX3G PLC using the USB port in PC. Re: communication with Mitsubishi PLC MELSEC in MC protcol. You can add a second RS422 port with a BD board or a add-on Block. The red programming cable has a converter in it that converts from RS422 to RS232 so you can connect to your com port on the computer. The “front” port where you plug in the programming cable is RS422. Really confused which communication is suitable for our device.There is a difference on what port you use on the fx PLC. configuring the Mitsubishi PLC to be a client to initiate MC Protocolcommunication commands to a MC Protocol server for connection handling and data transfer. There are two versions of protocol: one is with ASCII codes like BR, WR etc, and the other one says register address to be multiplied with 2 and convert to Hex and then ASCII. The protocol specifies only the serial commuincation(don't know how can I use USB connectivity PC(USB)-PLC(USB)).Ģ. We are OK programmers to programe in C#, the only thing is that we have downloaded the protocol, and there are two points:ġ.
#Mitsubishi plc serial communication protocol Pc#
And as far as connectivity, the PC is pretty close to the PLC and the application is for EOL test application, so Customer is ok with continuing USB port alternate. All ethernet options are really expensive and customer does not want to spend much on migration activity. I think with this restriction, option of using Modbus based hardware module(I am not too sure if the existing registers can directly mapped with Modbus option). One thing which we don't need to do is "Changing the PLC program". The existing application is connected to the PLC using USB port and is using a COM(I guess) component FXCPUUSB to communicate with the registers of the PLC. From the Protocol drop-down list, select your communication protocol: Ethernet Native String,Serial Native String, SLMP or SLMP Scanner. From the Manufacturer drop-down list, select Mitsubishi. In the Device Setup group box, from the Device drop-down list, select Robot.
#Mitsubishi plc serial communication protocol windows 7#
Actually in the current project, we are tasked to migrate a test application(VB 5.0) running on WinXP, which communicates with FX3G PLC to Windows 7 environment. In the Communications group box, press the Add Device button. That will be really useful info, especially when we will be developing a new solution. And last there is USB port, but USB is not solution for industrial environment. Problem is that good RS232 to RS422 converter or USB to RS422 converter cost as much as FX3G-485-BD and you loose port for online monitoring. Like previous but with this you need to have good programing skills. Interface module mounted on front of PLC. If you don't need high speed and you are not experienced programmer, but you still need equipment for harsh environment this is choice. RS485 adapter with integrated Modbus support. Very good solution if you have OPC or SCADA with drivers. I-Serial Communication fod00155 tha LED 21.2 LED LED QJ71C24N MC qnmao qnmao qnmao qnmao qnmao CHI RUN NEIJ.

Ethernet ADP module, MELSOFT, MC protocols, direct connection & data monitor. FX3U-ENET-ADP - Mounted on the left side. This is the best solution regarding quality. FX3U-ENET-P502 - It has everything including Modbus TCP/IP. Still you can do some tweaking if you have good router and have Modbus. Limitation is that you can't access to port 502, and that is standard port for modbus communication. classical FX3U-ENET - Ethernet communication module 10/100BaseT, TCP/IP, UDP, POP3, SMTP.
